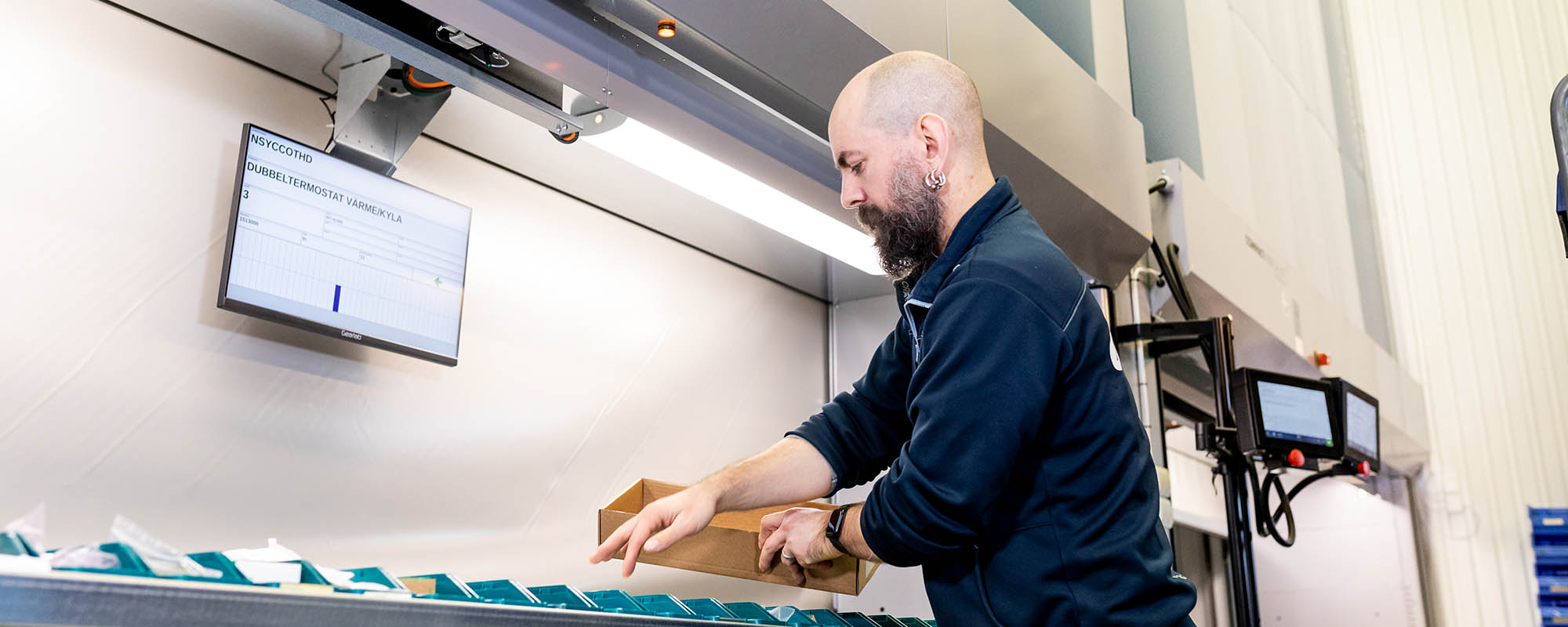
The right picking solution = easier, faster, and fewer errors
It’s not enough simply to be able to pick items quickly from a vertical storage lift. You also need to create the conditions that allow the operator to quickly find the right picking box to pick those items to so that they can make progress in their work. We have two pick-to solutions to choose from: Put-to-light and Put-to-screen.
Both solutions make it possible for one person to make a large number of order picks per hour without any difficulty. Which of our pick-to solutions are best for your business depends on the type of products you deal with and your warehouse management processes.
Put-to-Screen
A picking solution for highly variable items
Put-to-screen is a dynamic solution for multi-picks involving very different items. The operator can choose how many orders are to be started at the same time. This means that if five different orders contain the same item, they can all be picked when the tray is exposed in the handling opening. A display located behind the picking boxes shows to which box each item is to be picked, as well as details of to which order an item belongs and the quantity. The system keeps track of everything, enabling the operator to work at a high tempo, without stress or worrying about making picking errors.
> A completely dynamic system
> Multiple orders can be started at the same time
> Scanner acknowledgment ensures a high level of security
> Fast order line output
> Built for businesses that handle a wide variety of items
> A flexible picking system
How Put-to-Screen works
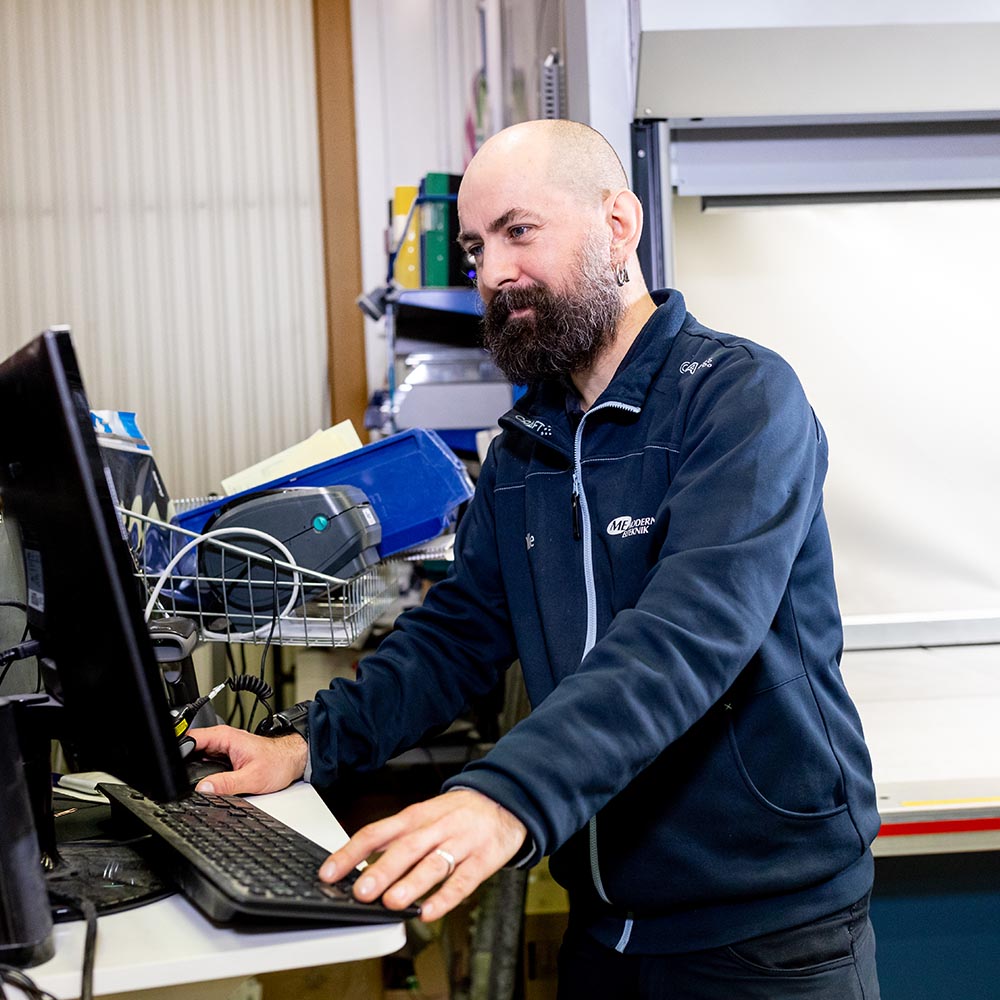
1. Order started
The operator starts a number of orders between 1-172. This is pre-selected in Compact Store. The system shows order number, item number, quantity, and the location from which the item is to be picked.
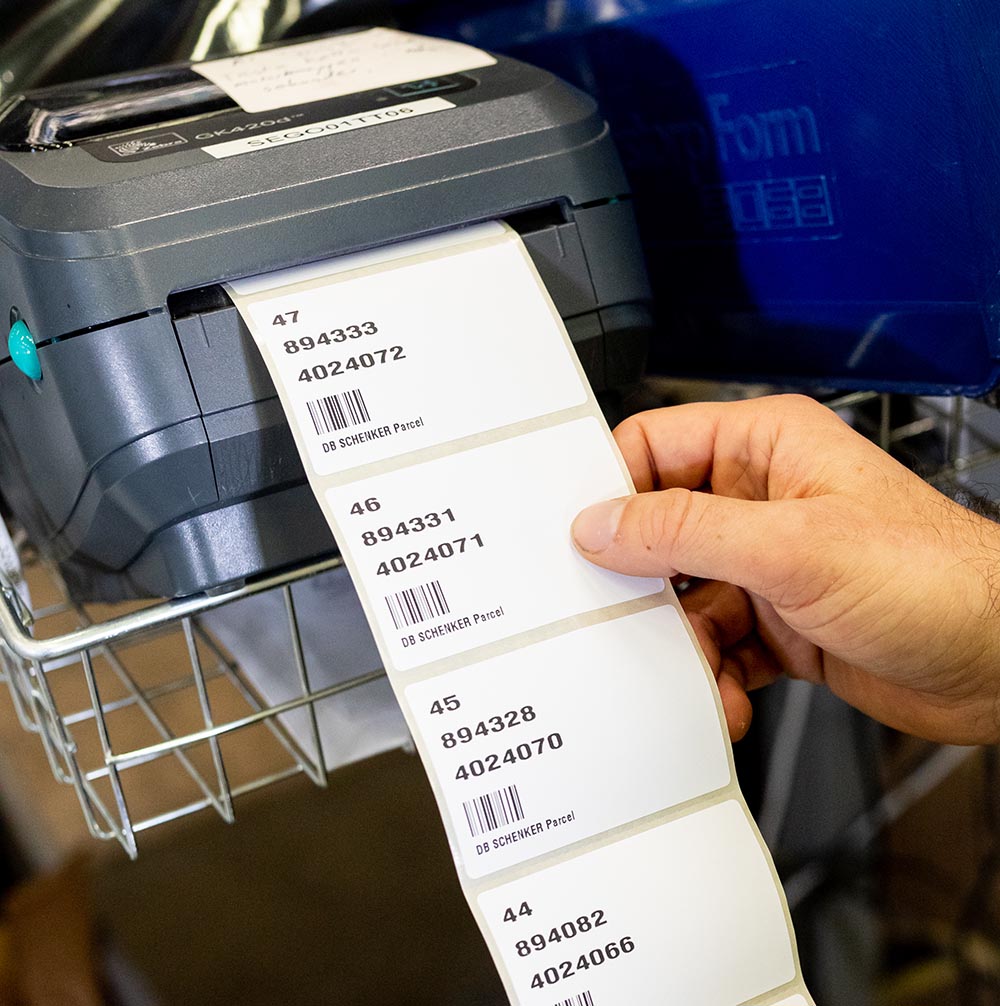
2. Acknowledgment label printed
The label contains order information and an EAN or QR code.
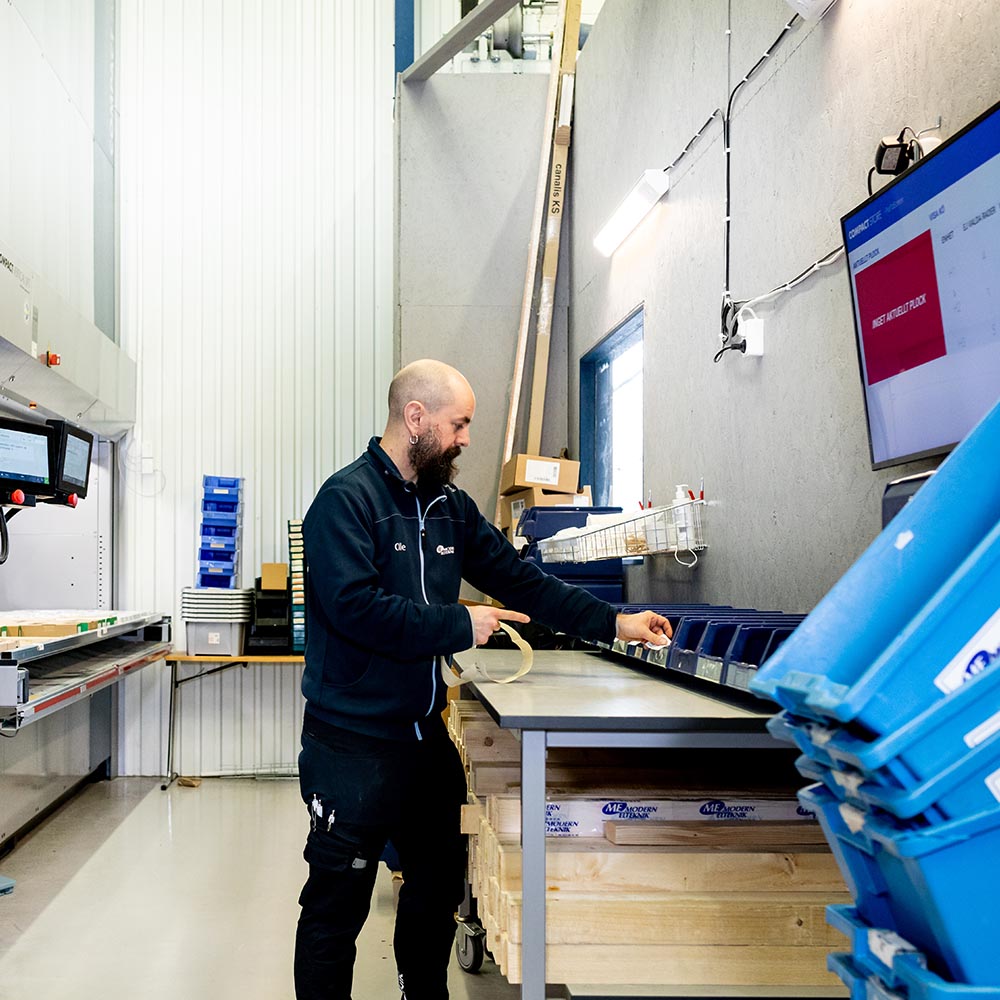
3. The label is placed at put-to-screen
The label is attached directly on the finished goods box or packing box for consolidation with other items.
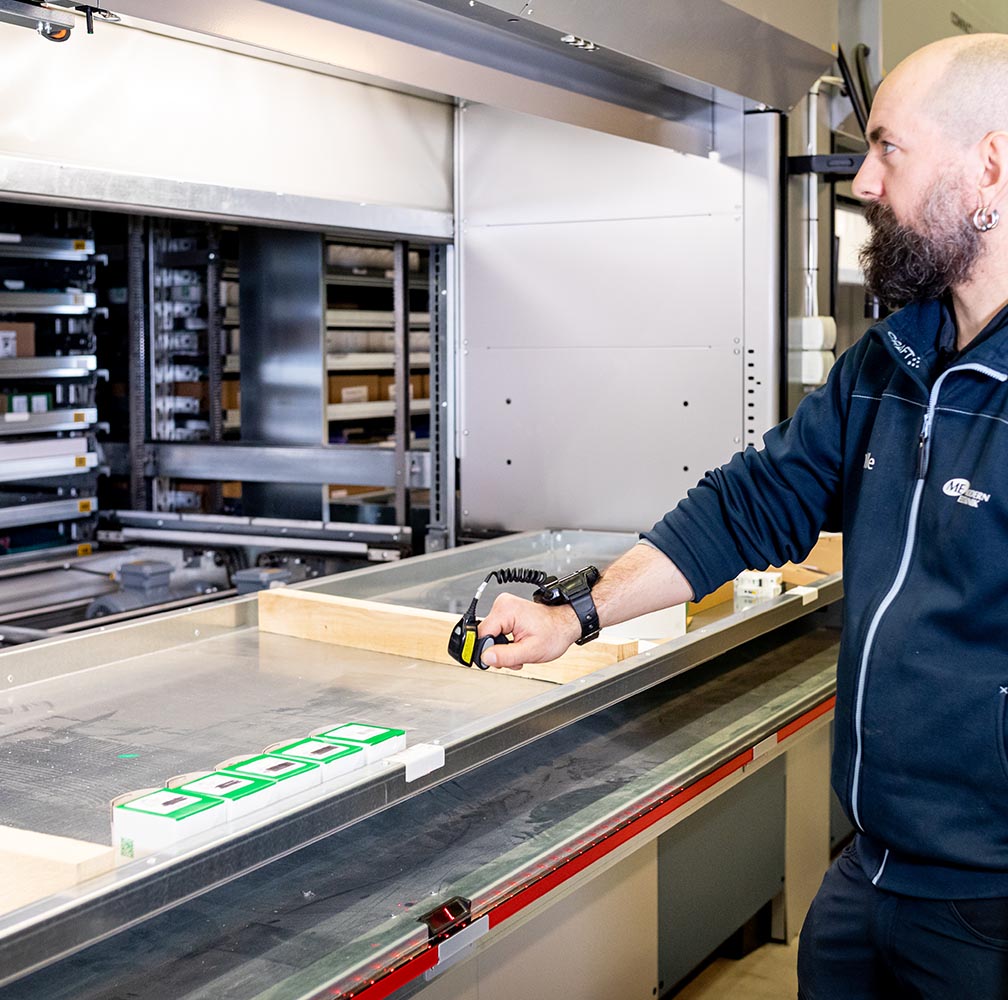
4. Item is picked from the vertical storage lift
The quantity of the ordered item is shown in the pick display and is taken from its storage location on the load tray that has come to the handling opening. The pick is acknowledged with a scanner or foot pedal.
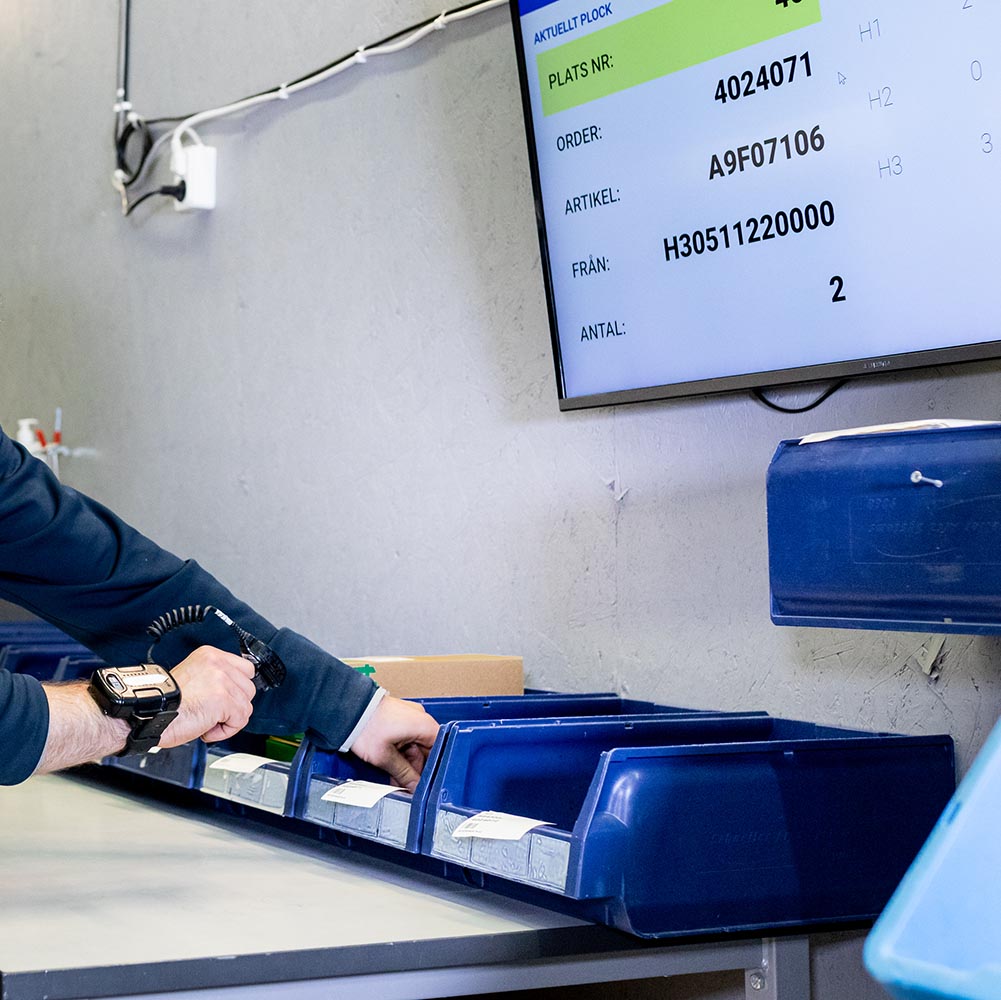
5. Item is placed in the pick box
Put-to-Screen provides information about quantity and in which box the item is to be placed. Each order line is acknowledged using a scanner.
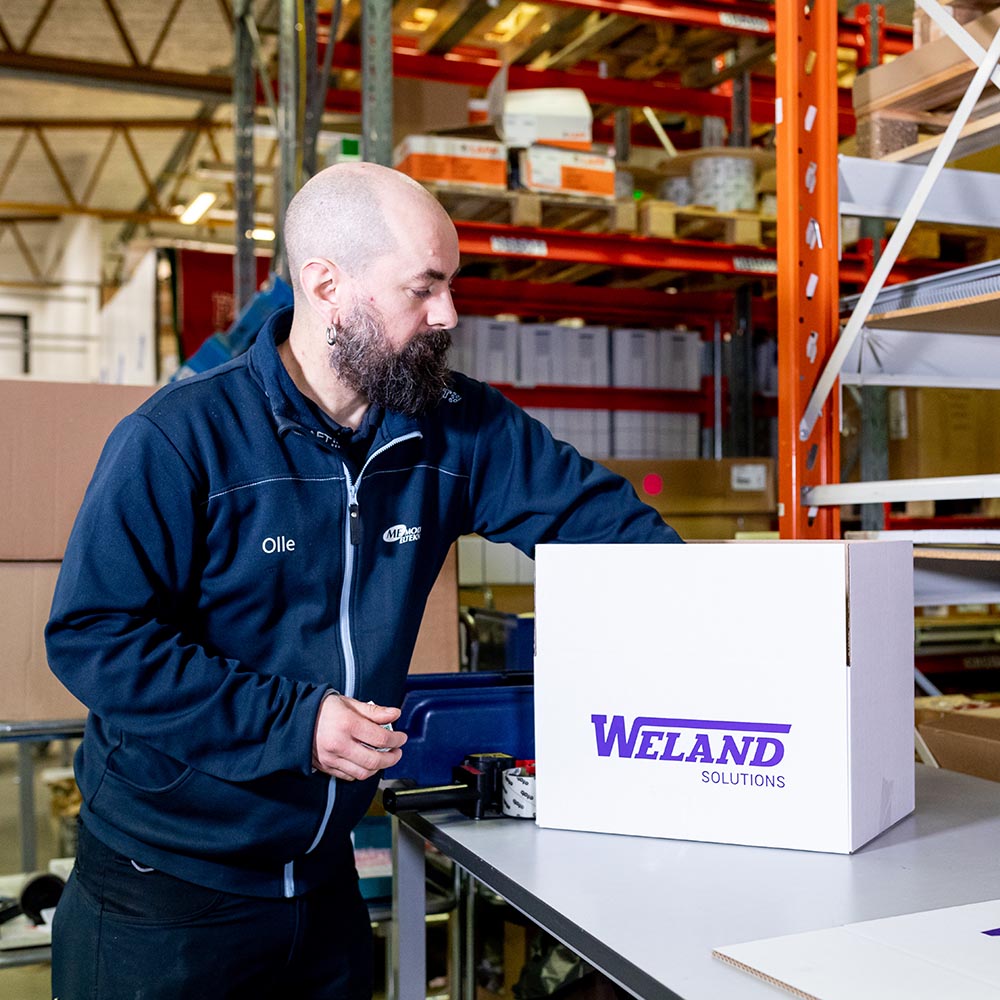
6. The item is moved to consolidation/delivery
The order is complete.
Put-to-Light
A picking solution for multiple instances of the same item to different orders
An efficient and quick solution for multi-picks in instances where the operator has to pick one type of item that forms part of several customer orders. Put-to-Light shows which customer order the item is to be placed in once it has been picked from the vertical storage lift. A flashing light shows the right box, and the LED bar provides an indication of the quantity. The added item is acknowledged by pressing a button on the display.
> A more static system where the same type of item and order is the norm
> Multiple orders can be started at the same time
> Easily acknowledged with a button push
> Fast order line output
How Put-to-Light works
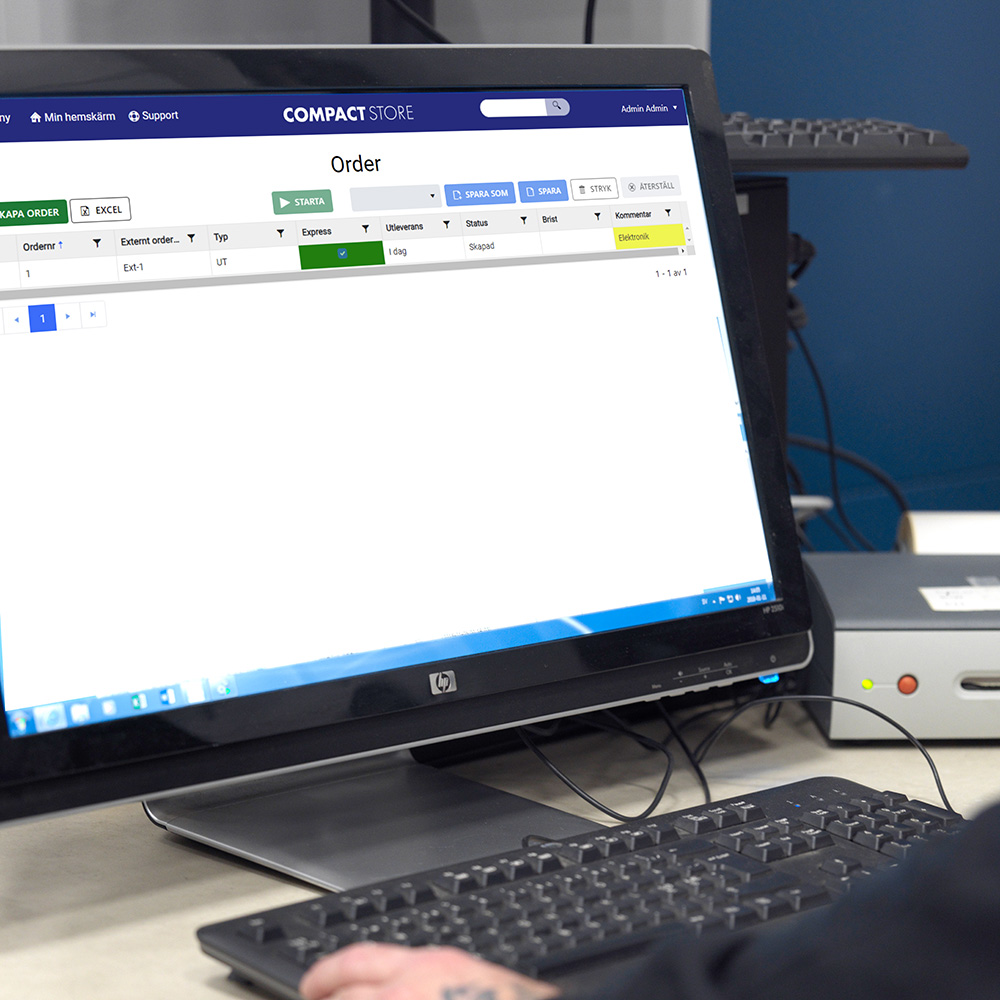
1. Order started
The operator starts a number of orders in Compact Store. This can vary between 1-172 orders, depending on how many Put-to-Light stations are available.
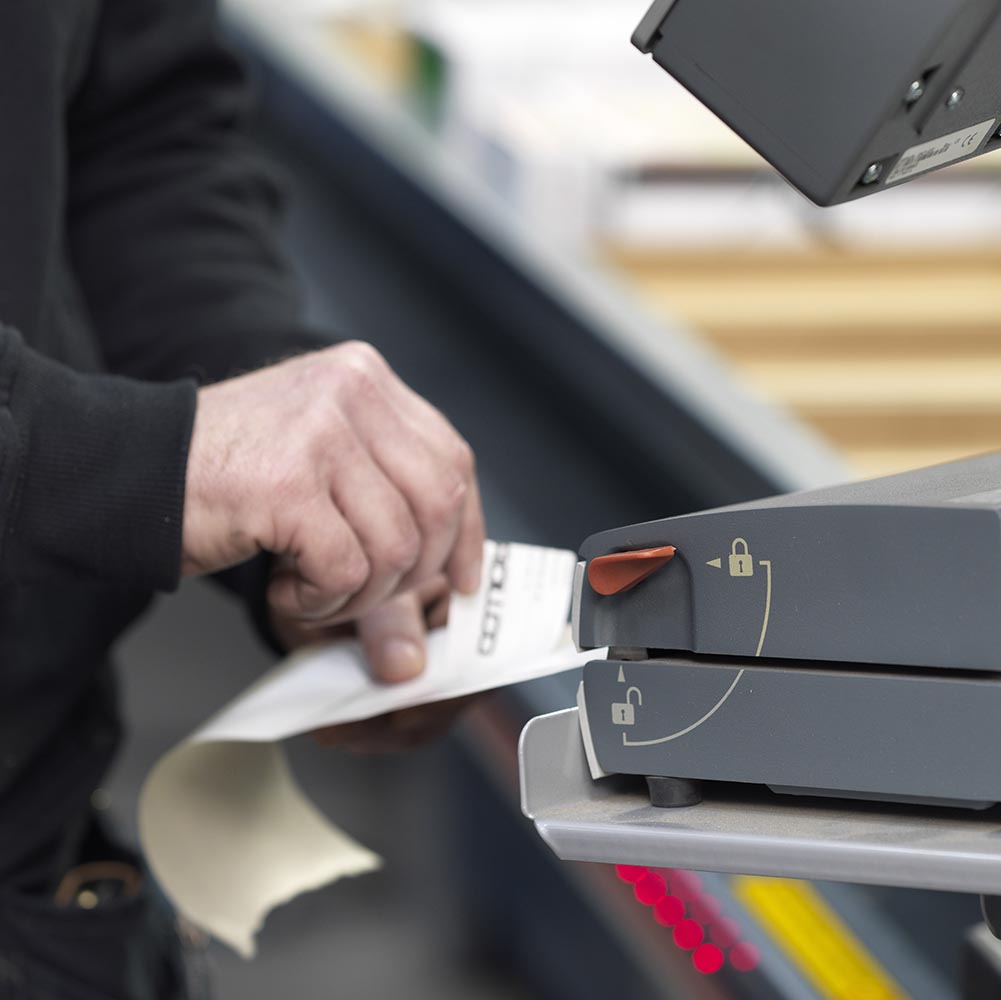
2. Acknowledgment label printed
The label contains order information and an EAN or QR code.
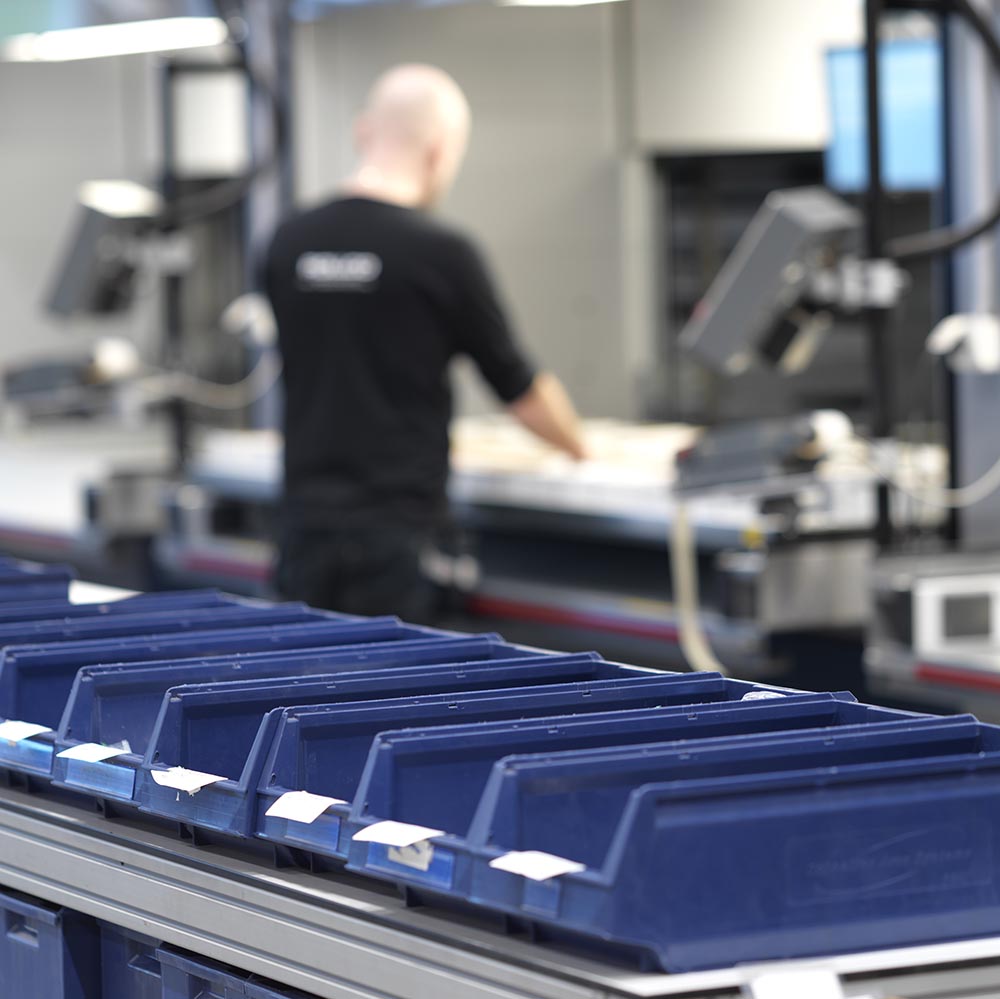
3. The label is placed at Put-to-Light
The label is attached directly on the finished goods box or packing box for consolidation with other items. The boxes are placed at Put-to-Light.
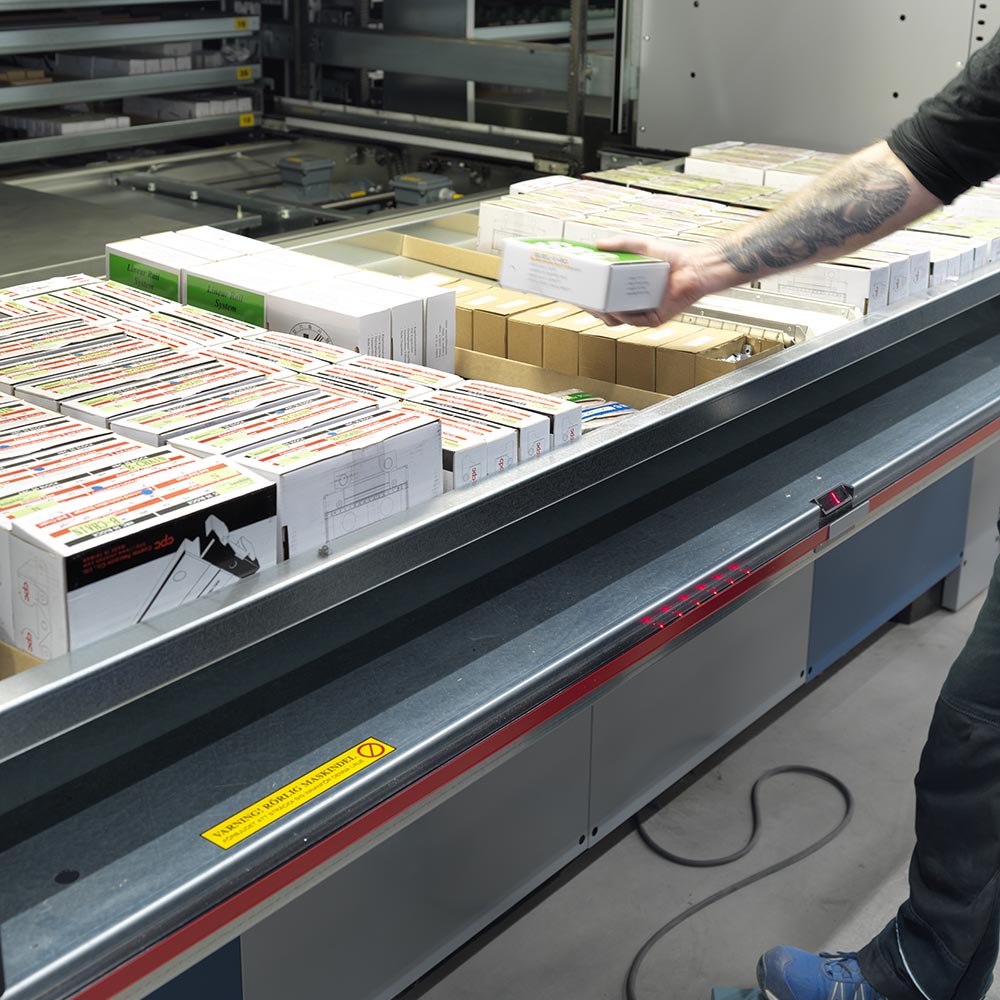
4. Item is picked from the vertical storage lift
The quantity of the ordered item is shown in the pick display and is taken from its storage location on the load tray that has come to the handling opening. The pick is acknowledged with a scanner or foot pedal.
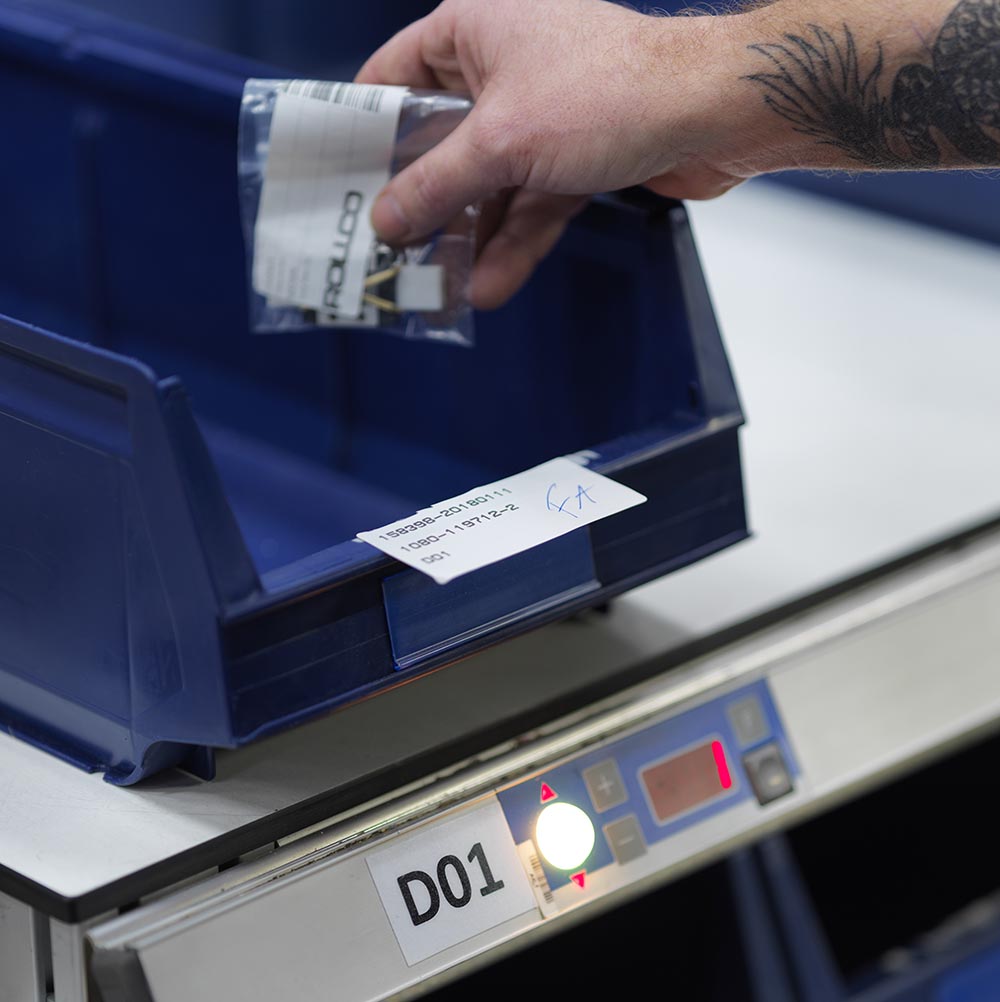
5. The item is placed in the picking box at Put-to-Light
Put-to-Light provides information about quantity and in which box the item is to be placed. Each order line is acknowledged with a button push.
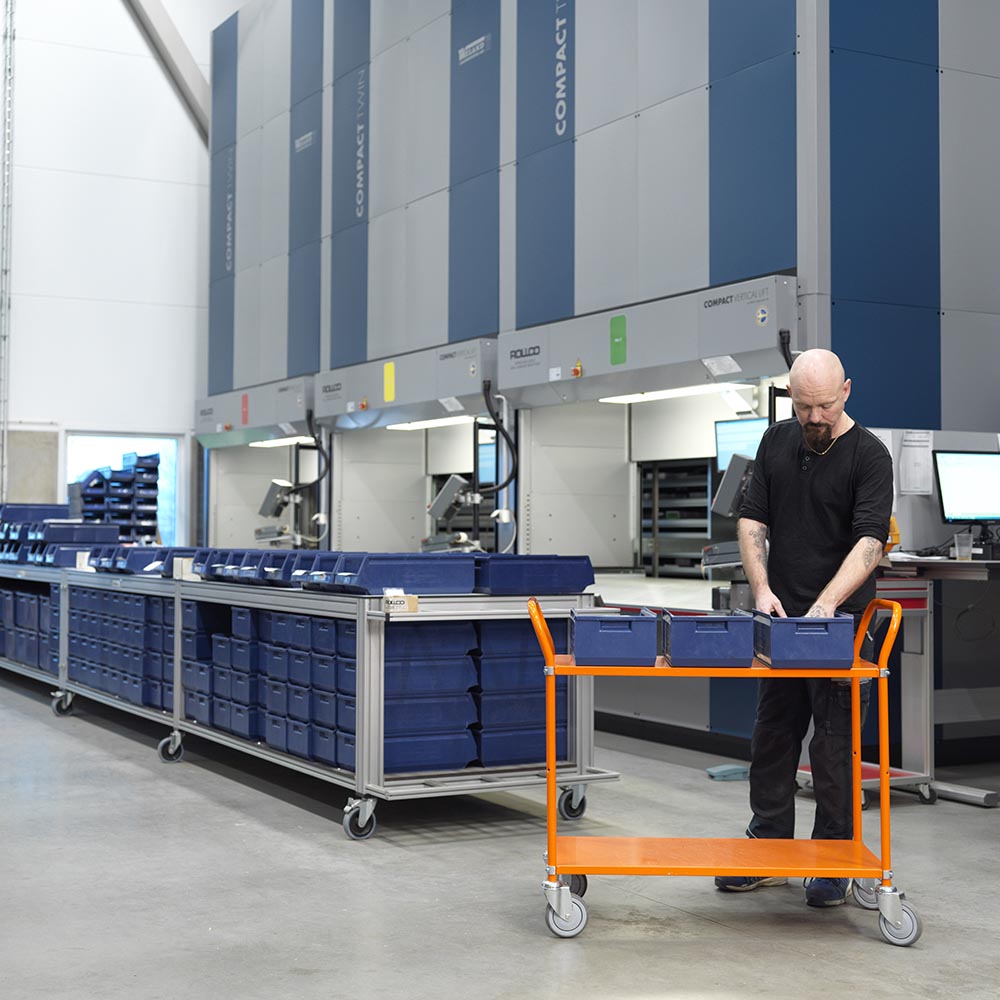
6. The item is moved to consolidation/delivery
The order is complete.
Item number | Designation |
FPUTTOLIGHT | Complete Put-to-Light rack |
Multi-pick increases efficiency even further
Compact Store creates opportunities to increase picking efficiency even further through multi-pick. The system enables you to calculate the best way to store items in the vertical storage lift so that Compact Store can sort orders into groups and deliver them to the handling opening on the same tray. This means that the operator can start and pick multiple orders at the same time with a very high level of efficiency. Whilst picking is taking place, the system prepares the next group of items to be sent to the handling opening as soon as the previous group has been confirmed by a button push from the operator. In this way, the operator avoids having to wait unnecessarily for the vertical storage lift and has total control over picking speed.
The multi-pick process
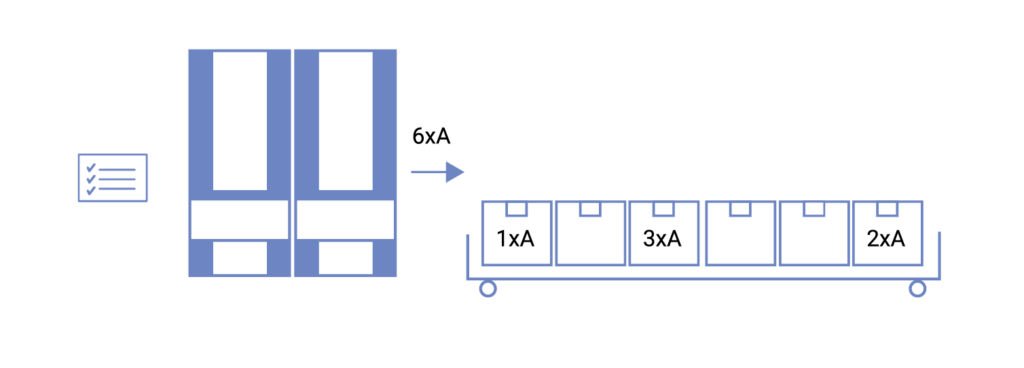
- 6 x item A are picked from the vertical storage lifts.
- These are then split across three different customer orders as follows: 1 item, 3 items, and 2 items.
- Once the operator takes the items from the vertical storage lift and turns towards the picking solution, the display clearly shows in which picking boxes (orders) and the quantities into which the items are to be split.
- Acknowledgment by scanner or button push minimizes the risk of picking errors.